Metalizing
All About Metalizing
Montana Metalizing offers the most environmentally friendly, productive, and economical form of galvanizing and corrosion prevention offered today.
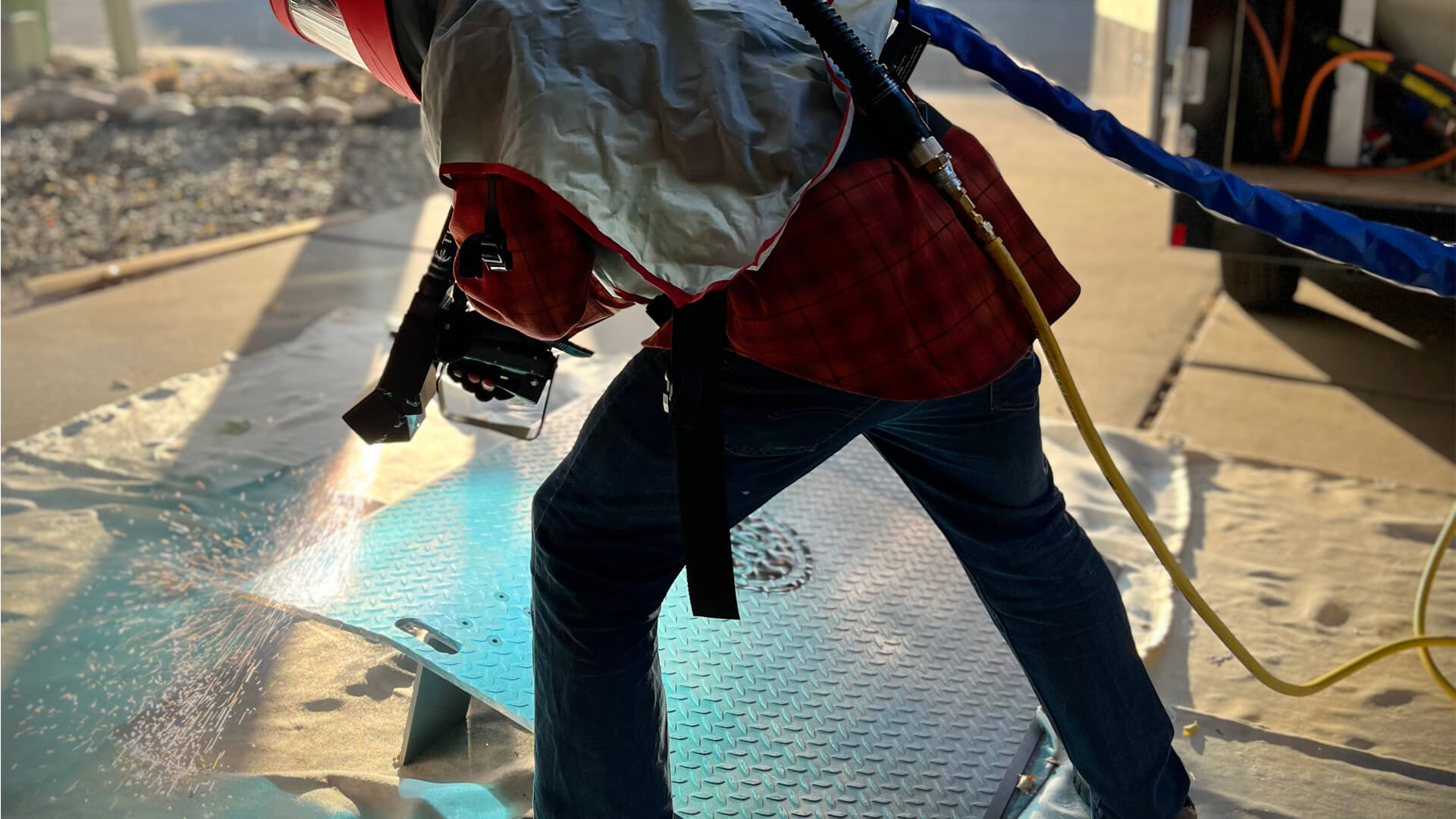
The process starts with surface preparation. Montana Metalizing uses an electric arc as its heat source to melt the solid wire into a sprayable molten state. The molten metal is then propelled and atomized into the specified spray coating. The coatings are applied at a thickness of 1-3 mils thick, and built-up and layered as specified. Metal coatings have unique characteristics that make the applications limitless and can be applied in any industry. Please see the Applications page for details and benefits of various applications.
Benefits Of Metalizing
Environmentally Friendly & Cost Effective
Montana Metalizing delivers the most environmentally friendly, efficient and economical galvanizing and corrosion prevention technique currently available:
- No environmentally harmful Volatile Organic Compounds (VOCs) — like those found in the majority of paints and solvents
- A Single coating treatment is designed to last for decades, does not chip, and does not require touch-up or maintenance — for a highly cost-effective life-cycle
Unique Properties of Non-Skid and Wear-Resistant Metal Coatings
- Minimum of 10+ years’ life cycle, in continuous operation, based on studies conducted by the Navy
- Zero cure time and ready for immediate use
- Non-skid coatings ideal for refinery decks, vehicle ramps, loading docks, forklift loading ramps, aircraft landing & loading areas — or any application seeking both corrosion protection and non-skid properties
- Zero Volatile Organic Compounds (commonly found in aerosols and paints)
- Impenetrable by oils, solvents and oxidation caused by high salinity (i.e. salt water)
- Dual purpose coating with superior corrosion protection and non-skid properties
- Lightweight in comparison to other non-skid coatings at lbs. / ft² (Aviation advantage)
- Has exceeded all US Navy testing requirements as per MIL PRF- 24667:
- “MIL-PRF-24667C, NON-SKID COATING SYSTEM for SPRAY APPLICATIONS - (22 MAY 2008) [SUPERSEDES DOD-C-24667, MIL-D-23003 & MIL-D-24483]., This specification covers non-skid systems, coatings, and coverings for application to weather decks, flight decks, and hangar decks of air capable amphibious aviation and aviation ships. Coatings are applied to steel, aluminum, reinforced plastic, and special hull treatment (SHT) surfaces by spraying, rolling, or other application method as designated by the manufacturer of the non-skid system. “
~ Source: EverySpec.com>Library
- “MIL-PRF-24667C, NON-SKID COATING SYSTEM for SPRAY APPLICATIONS - (22 MAY 2008) [SUPERSEDES DOD-C-24667, MIL-D-23003 & MIL-D-24483]., This specification covers non-skid systems, coatings, and coverings for application to weather decks, flight decks, and hangar decks of air capable amphibious aviation and aviation ships. Coatings are applied to steel, aluminum, reinforced plastic, and special hull treatment (SHT) surfaces by spraying, rolling, or other application method as designated by the manufacturer of the non-skid system. “
Mobile Services
Our onsite mobile treatment allows for uninterrupted production with zero downtime and rapid restoration of equipment, materials and assets.
Cold / Low-heat Process
Unlike Hot Dip Galvanizing, our “Cold Process” coating and galvanizing involves lower temperatures and slower heat distribution in order to avoid potential warping and degradation — thus reducing the risk of distortion and damage to your assets.
Substrate Surface Preparation
Achieving bond strength and longevity in metalized coatings starts with adequate surface preparation, which is crucial for effective and long-lasting adhesion. Montana Metalizing achieves quality coatings by prepping each surface with our mobile sandblasting service before metalizing.
Minimal Maintenance Required
Metalizing services are designed to achieve optimal durability of surface coatings with minimal maintenance over the course of an industry-leading lifespan.
Extended Surface Coating Lifespan
While the life of a metalized coating depends on its environment and exposure, metalized coatings offer a far lower life-cycle cost while outperforming alternatives such as powder coating, panting and the brush-on zinc “galvanizing”.
These alternatives require touch-up and re-treatment, while metalized coatings do not. Metalizing can effectively do its job for several years or even decades, without requiring rework.
Instant Application Handling Time
Requiring no wait or cure time before handling or assembling, our “Cold Process” metalizing is safely warm to the touch immediately following application — for uninterrupted usage and productivity.